From athletes to machines: How to ensure manufacturing optimization
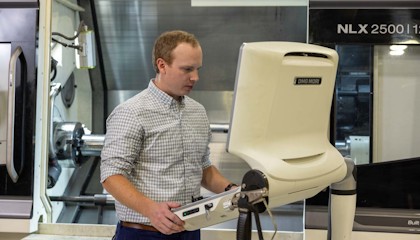
In the world of sports, the addition of a star player joining a team is often seen as a strategy to boost performance.
The same principle applies to the corporate world, where companies invest in expensive software solutions with the goal of achieving manufacturing optimization.
5 tips to improve shop floor management.
In this blog, we dive into the parallels between sports teams signing star players and companies adopting new digital manufacturing software solutions. We'll explore the critical role historical performance plays in decision-making, as well as the disappointment that can arise when expectations aren't met.
We will examine the importance of a strong foundation in both scenarios. Just as a sports star's success depends on the cooperation of their teammates, the effectiveness of a digital solution hinges on accurate and complete information from the team. Using the example of Vericut, a renowned digital simulation tool for manufacturing, we'll illustrate how a lack of essential information can hinder success. We'll also share a real-world case study from MAB GmbH in Germany, demonstrating the positive outcomes that come from establishing solid digital practices.
Join us on this journey as we uncover the key to unlocking success, not only in acquiring star players or innovative software solutions but also ensuring the environment they enter sets the team and shop floor up for success.
Understanding the parallels
When a sports team acquires a star player, the expectation is that the team’s performance will be measurably improved. So many teams wonder, why would management choose to sign a new player to an expensive contract if they weren’t going to significantly improve the team’s performance?
And that same thought happens all too often with companies spending time and money on a new software solution.
The importance of historical performance
Historical performance is a large factor in making this decision; to a team who has trouble scoring goals, acquiring a player who has historically scored a lot of goals seems like a good solution to the problem. And this same applies to the world of manufacturing, a company who encounters unexpected problems on their machine may invest in a solution that has been proven to catch these problems digitally before they happen in the real world.
On the other hand, sometimes these signings or investments do not yield the expected results.
Leaving you wondering why the new player is scoring only a fraction of the goals than in previous seasons? Or in manufacturing, why are issues still being encountered and not caught beforehand?
This is where the player's historical performance becomes essential, or in the digital solution case, has historically been proven effective for numerous customers. However, what distinguishes the successful cases from the unsuccessful ones?
The limitations and foundations of success
Both the sports player and the digital solution share a common limitation – they can’t compensate for foundational weaknesses. If the teammates of the new player are unable to work together, it’s hard for the player to produce the expected goals. And just like the new player’s effectiveness depends on the cooperation of their teammates, a digital solution success hinges on being provided with accurate and complete information, otherwise it’s not able to correctly identify problems.
When the player or solution does not meet expectations, both are likely to be blamed. Before accusing either the new player or the solution of being the wrong fit, we must consider the environment they are entering.
Choose a product to digitally simulate machining operations
Vericut is a product used to digitally simulate machining operations to catch problems before they occur, just like a star player referenced earlier.With a 40-year history of proven success, it is often called upon when machine stability, efficiency, quality, or output need improvement. For these areas, Vericut is the go-to solution. However, if it is not supplied with the necessary information, it is not able to deliver the expected value to customers.
Many of the customers who are looking to purchase Vericut, also use a CAM system to create the toolpaths necessary to machine their parts. In this workflow, the user would go from creating their toolpaths in a CAM system, then use Vericut to simulate the toolpaths before sending to the machine that will use these paths to machine the required part.
Vericut, simulation to ensure manufacturing effectiveness.
The intention of this simulation is to ensure no issues occur when the part is running on the machine. To accomplish this, Vericut must have all the necessary information to ensure the digital world created matches the physical world exactly.
Vericut has worked closely with CAM providers to create easier ways to transfer this information, mainly through integrated plug-ins. However, if this information does not exist in the first place there is nothing to be transferred. Other times the information exists, but it is not defined in the way necessary for the Vericut plug-in to automatically recognize it.
We often assume that because a customer is using a CAM system, they are doing so in the ways recommended by the software provider. Some examples relevant to Vericut include:
- Defining the machine being used.
- Defining the coordinate systems being used.
- Defining the model of the starting piece of material (stock).
- Defining the model of the part being produced.
- Defining the model of the fixture being used to hold the part in the machine.
- Defining the models of cutting tools and cutting tool holders.
Everything listed here is the components required for Vericut to accurately replicate and simulate what will happen in the physical world. It is possible (and recommended) to define these items in the CAM system and when this is done correctly, Vericut can automatically recognize these items and correctly define them for simulation. But what happens if these items are not correctly defined, or if the models are not being used at all in the CAM environment? They will not magically appear in Vericut, they still must be defined. Just as a star player will not succeed without support from their teammates, Vericut will not succeed if it is not supplied with the correct information.
A real-world example – MAB GmbH
MAB GmbH, a batch production facility located in Germany, is a good example of what we imagine when we picture a smooth implementation that yields the expected results. MAB wanted to increase the efficiency of their 5-axis Hermle milling machines, some of the most complex in their facility. As MAB produces many different parts in relatively low quantities, it was determined to find the best way to reduce setup time and reduce unplanned downtime caused by program errors.
MAB has long used Hypermill to program these machines, but more importantly is they established ways-of-working for the CAM programmers that ensures solid models are used for all components that will exist in the physical world, as well as defining these in the proper way in Hypermill (the digital world.)
MAB implements Vericut to achieve optimal efficiency.
This was not a small task, as the solid models for fixtures and tools had to be downloaded from suppliers or designed by the programmers. Once the models are acquired, they are properly stored in their respective libraries so all programmers can easily access them. When a new program is started in Hypermill, the programmers are trained to use and define these components every time. Because of this work MAB completed to establish these libraries and become knowledgeable on how things must be defined in their chosen CAM system, there was very little work MAB needed to do to begin using Vericut to achieve their desired benefits.
MAB joins forces in the Sandvik Lighthouse Program
Building a strong foundation
It is important to remember that customers who may not be as digitally mature in the CAM area does not mean they are not competent. It could be easy to assume that if a CAM department is not using solid models or is not defining things correctly in their CAM system that they are not competent programmers, but this would be incorrect. Users will resort to whatever process or tool they are most confident in to produce the required results to meet their deadlines. Creating libraries and establishing proper processes can be time consuming, but it is an essential foundation to build on to be able to realize the expected benefits of many of the digital solutions available to manufacturers today.
Unlocking success
In the end, it becomes evident that the key to unlocking success lies not only in implementing an all-star player (human or digital), but also ensuring the environment in which they operate has a strong foundation.