The importance of integrations in automation
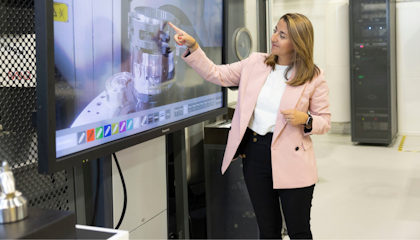
How introduction plays a major role in automation.
Why product integration and automation are important to Industry 4.0?
The use of product integration and automation in the manufacturing industry is important to improve factory floor efficiencies and reduce human errors – by moving humans to less repetitive tasks and reducing data errors.
In this blog you can explore benefits and examples of how production integrations play a major role in automation.
Benefits of product integrations in manufacturing
Product integrations in the context of manufacturing refers to various components of software working together, from different industry sectors, to complete a final product or manufacturing process with benefits such as functionality, efficiency, and connectivity.
As industries continue to embrace digital transformation and automation - integrations will likely play an even more significant role in shaping modern industrial processes.
Integrated systems play a crucial role in streamlining operations and improving overall efficiency on the factory floor in several ways.
- They provide a holistic view of manufacturing operations.
- Enable automation and data-driven decision making to reduce downtime.
- Improve product quality and enhance overall efficiency on the factory floor.
Integrations are essential for manufacturers to remain competitive in today's fast-paced industrial landscape.
A few examples of integrated manufacturing include (but are not limited to), Sandvik Coromant CoroPlus® Tool Library, which has integrated with Cimatron, GibbsCAM, Mastercam. And another integration example is GibbsCAM and CGTech’s VERICUT, all helping to prevent shop floor errors.
How integrated systems allow for uninterrupted exchange of data?
Integrated systems allow for seamless exchange of data between different processes and equipment on the factory floor often evolving automation of various tasks and processes.
They also reduce the need of manual labor and minimize the risk of human error, because automated systems can perform repetitive tasks consistently and efficiently leading to higher production rates and improved product quality.
There are several common misconceptions about product integration and manufacturing that can hinder their adoption and effective implementation, it should be a strategic decision that aligns with your organization's goals and resources.
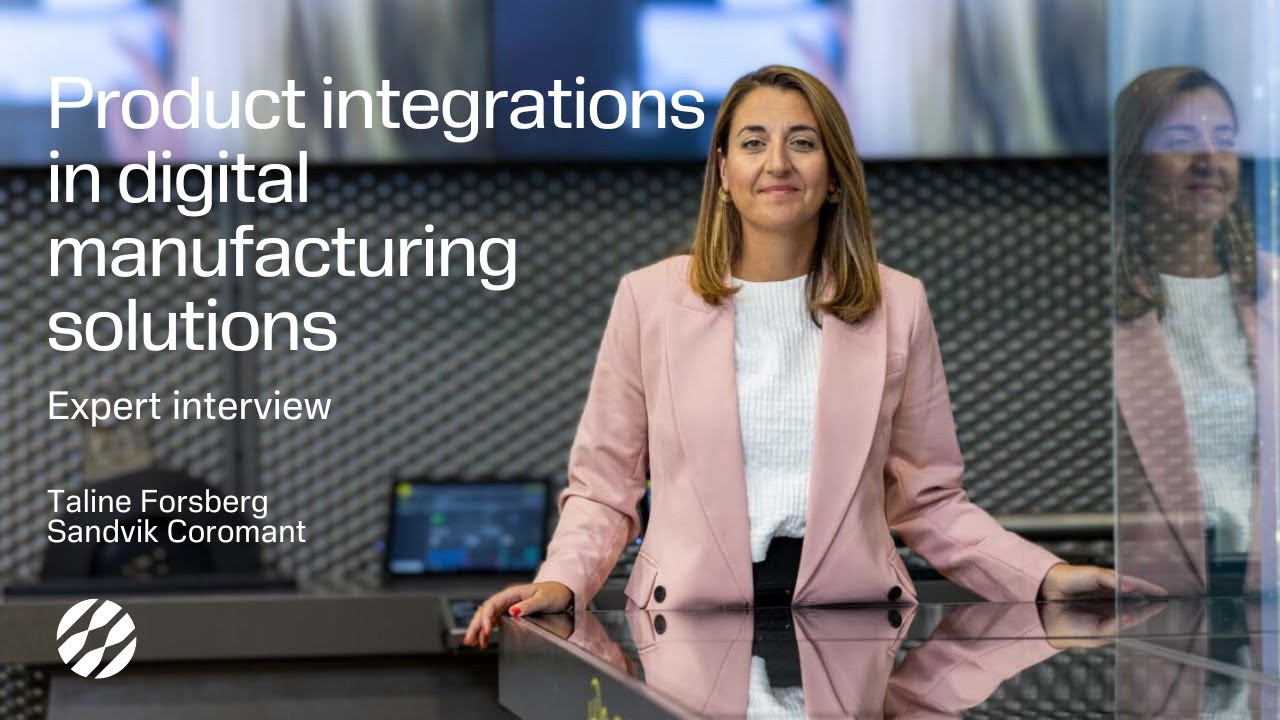
Common misconceptions about automation
The most common misconception is that it's too expensive, while there can be upfront costs, these investments often lead to long term cost savings.
The other is that it’s only for large enterprises, and some believe that product integrations are suitable only for large manufacturing companies.
Another misconception is that integrations are too complex, or very complicated and technically challenging requiring a lot of change.
However, many integration solutions are scalable and can be tailored to the needs and budget of smaller enterprises. But they can also be done in one defined specific area and the change can be made incrementally.
Also, many people think that integrating systems processes or machines will eliminate jobs - while it may change in nature of certain roles - integration often creates new opportunities for skilled workers who can then manage and maintain integrated systems, analyze the data, and optimize processes.
How integrations and automations reduce human errors?
Product integration helps manufacturers reduce manual work and human errors in their operations.
This is made possible by automating repetitive tasks and processes while making the decision-making process more fact than databased.
Integrations make testing and verifying process steps already in the design stage rather than in an actual machine on the production floor. These all help to reduce the reliance on manual work and minimize human errors.
Automation not only enhances efficiency, but also improves product quality and reduces operational costs, which is a significant driver of competitiveness in the manufacturing industry.
A successful product integration includes a step wise approach
Successful integrations can enhance productivity efficiency and internal competitiveness. However, to see the advantages of integrations and not burn the organization out, I suggest doing it in steps.
This stepwise approach helps to understand the need of integration, as well as expected needs of improvement prioritizing tasks in order of relevance, and time to market cost of goods sold.
Understanding the cost implications both regarding time and running costs are particularly important to avoid surprises.
When you’re further down the road, the most important thing is to have buy in from the organization by embracing integration as a strategic imperative.
This way you can position your organization for success in an increasingly connected and data-driven world.
Key takeaways for product integrations
- Understand why you're doing it.
- Who is going to be involved and affected in the long run?
- Understand that success factors include long term to know the cost implications.
- Understand what it's going to cost in the short term, but also the gains for the long term, as well as the running costs.