How tool data is the new energy: Tool data management
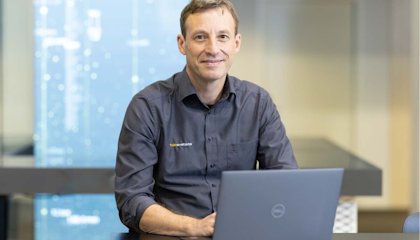
TDM Systems transforms big data into useful information to power next generation smart manufacturing
The data revolution
Just as energy was essential for past industrial advancements, today, data has become a critical resource. As energy in various forms powered past industrial revolutions, data now drives the modern revolution.
This modern revolution, Industry 4.0, data can be collected from various sources such as sensors, machines, and processes that are harnessed to make informed decisions, optimize operations, and create innovative products/services.
Data is the fuel powering these advancements - transforming the next generation of industrial revolutions.
However, big data by itself is not providing meaningful insights. Proper processing, analysis and interpretation are essential to draw conclusions to make informed decisions based on the available data.
For example, tool management systems such as the TDM System are essential systems to collect and process raw data into useful information.
This includes collecting and distributing data, enhancing and processing data, data analysis and visualization, and of course interpretation and analysis along the entire end-to-end manufacturing process.
Industry 4.0 data is collected from various sources like sensors, machines and software along the entire end-to-end manufacturing process. This data serves as the foundation for making informed decisions, optimizing operations, and creating innovative products and services.
Think of it as the fuel powering the advancements and transformations of this fourth industrial revolution. However, having massive amounts of data is just the beginning; what's essential is how you process, analyze, and interpret the data to derive meaningful insights, and decisions.
So, what are the details of tool management data becoming the new energy for manufacturers?
How can tool data management systems boost competitiveness?
Enter tool data management systems. These systems ensure you have the necessary information about your tools at your fingertips.
From stock levels and assembly drawings to toolkits, preset data, and setup sheets, they make sure you have the right tool at the right time and in the right place. The results are reduced process defects, minimized machine downtime, and increased efficiency.
These systems can monitor the actual tool life of the cutting tool on the machine, compare it with a nominal value, provided by the programmer, and when it hits a warning limit, initiate a tool change, and ensures your production line keeps humming smoothly. As a side effect, enabling you to adjust, optimize, and evaluate the quality of your cutting tools, and your cutting tool suppliers.
But the benefits go far beyond this. A high-quality digital twin created by these systems saves time in programming, improves simulation quality, and enhances the final product, especially in small-batch production. They can even manage "batch size one" processes.
Industrial state-of-the-art technological advancements
The next level of manufacturing is all about combining big data with real-time data and harnessing advanced analytics and AI.
These tools optimize asset efficiency, improve decision-making, reduce costs, and enhance quality. Studies have shown that organizations with strong analytics capabilities perform better financially, make decisions faster, and execute plans more effectively.
And this is where I am certain that AI (both the more “traditional” machine learning as well as generative AI) is the key to utilize big data, to make informed decisions, model and plan processes in real-time, optimize maintenance, maximize production, and control project costs.
These technologies drive innovation and improve operational efficiency, setting you apart from the competition.
Technology alone isn't the answer
While technology is essential, it's crucial not to get lost in the technology trap.
Flexible and user-friendly tool data management systems are the key. These systems should integrate seamlessly into your existing workflows and processes.
They are not just an IT function but a discipline in its own right. They need to interface with software like CAM and SIM, and even with hardware such as vending, presetting, and machines. In the era of real-time data, managing data overload becomes the biggest challenge. Sometimes, less data is more.
In the context of Industry 4.0, advanced technologies like the Internet of Things (IOT), cyber-physical systems, digital twins, and big data analytics offer countless opportunities for developing intelligent manufacturing processes. The key is to keep it smart and simple, tailored to your specific needs.
Typical obstacles and recommendations
When embarking on a digitalization project, don't lock yourself into closed systems. Interoperability and openness are essential. The manufacturing landscape often lacks interfaces and standards, so choose an open, flexible solution.
Define clear objectives for your project, focusing on real benefits, not just hype. Empower your people to embrace digitalization by offering training and upskilling opportunities. Address their fears and make them see digitalization as an opportunity to take on new challenges and career paths.
TDM highlights
The new energy of tool management and why it matters?
Tool data is the new energy that propels manufacturing to new heights.
By embracing the power of tool management systems, combining big data with real-time data, and staying focused on the practical application of technology, small to medium-sized manufacturers can lead the charge in the modern manufacturing revolution.